聞かせて先輩!
20年の月日をかけて。 後輩記者のTakeaway
"音響のエキスパート"を納得させる
再生プラスチックができるまで
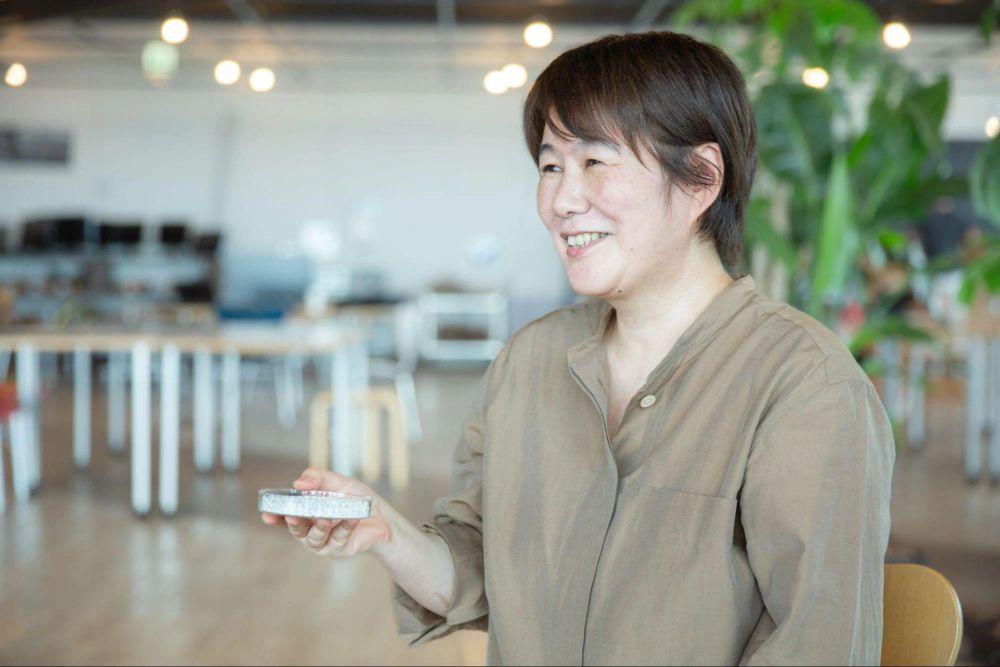
今をさかのぼること20年前。ソニーの伝説的なプロダクトとして知られるウォークマン® に、植物から作られた「植物原料プラスチック」が初めて取り入れられました。
この素材を世に送り出すにあたり関わったのが、入社時から一貫してソニー独自の材料開発に携わってきたソニー株式会社(SEC)の藤平 裕子さん。2019年には新たな「良音再生プラスチック」という新たな素材を開発し、ホームオーディオ製品に導入。優れた音質と、環境への配慮を両立させることは、開発一筋の藤平さんにとって大きなチャレンジだったといいます。
今回は藤平さんと同じく理系出身で、SECの調達業務に関わる小林 茉莉子さんが藤平さんにインタビュー。再生プラスチックの利用拡大にかける熱い思いや、知られざる開発秘話を聞きました。
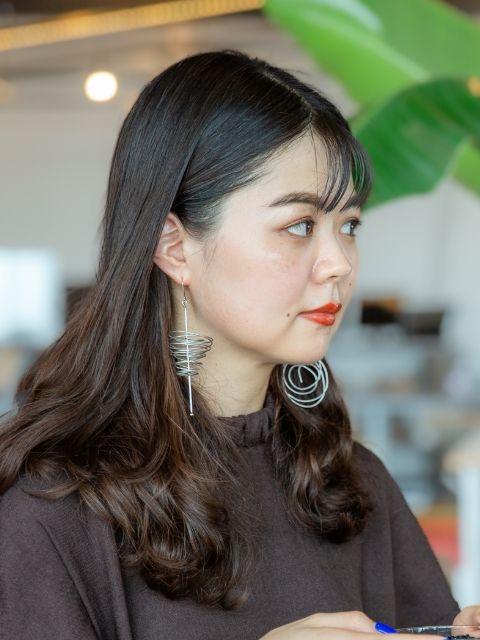
私がインタビューします!
小林 茉莉子さん
ソニー株式会社 調達センター ソーシング部門
2018年入社。SEC製品に使用される半導体部品の試作購買業務を担当。最近は環境やサプライチェーン関連のサステナビリティに興味があります。
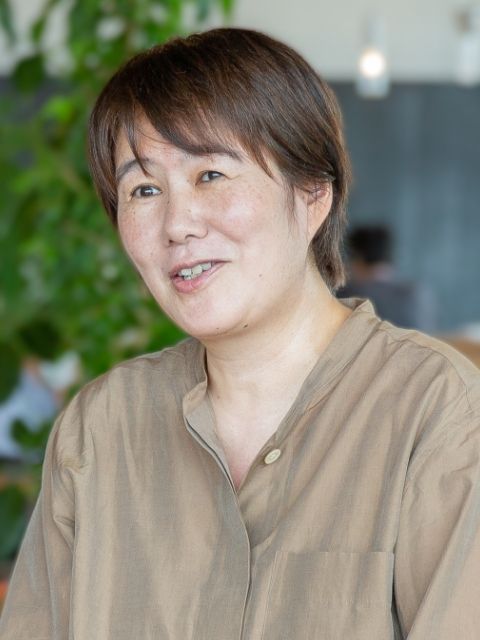
お話を伺ったのは…
藤平 裕子さん
ソニー株式会社 ホームエンタテインメント&サウンドプロダクツ事業本部 音響設計部門 設計1部
環境技術部にて10年以上バイオマスプラスチック・再生材の開発に従事。製品設計に異動後も一貫してソニーオリジナルの材料開発に係る。
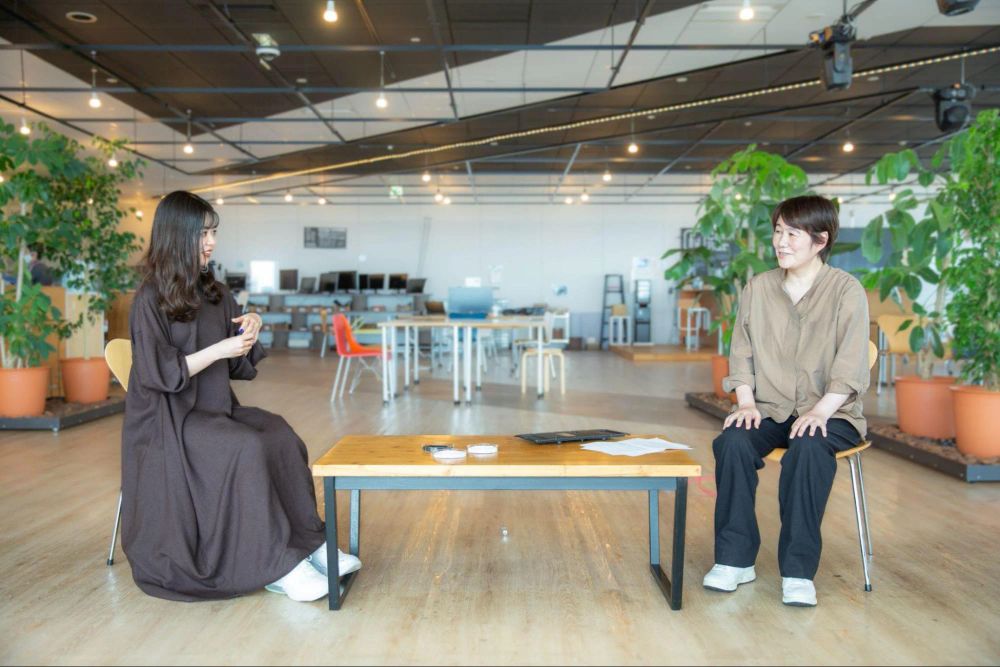
20年前のウォークマンに植物原料プラスチックを導入
小林:藤平さんは1999年に入社されてから、ずっと研究開発の第一線で活躍されている大先輩。同じ理系出身ということもあって、藤平さんのように働き続けられたら…と憧れています。
藤平:ありがとうございます。最初にお会いしたときは、小林さんの調達部のお仕事についていろいろ教えていただいたので、今日はなんでも聞いてください。
小林:藤平さんが最初に配属されたのは、R&D(研究開発)の環境技術部ですよね。
藤平:そうです。ちょうど入社したときにソニーで植物原料プラスチックの開発が始まり、そこに参画した形です。
今は世界的にストローが紙素材に変わったり、スーパーのポリ袋が有料になったりと、石油由来のプラスチックの使用を減らす動きが進んでいますよね。当時はその第一次ブームというか、環境問題が注目を集めていました。でもソニーは世の中が盛り上がる前から、環境に負荷をかけないオリジナル素材の開発に注目していたんです。それで、他社に先駆けて植物原料プラスチックを使った製品を作ることができました。
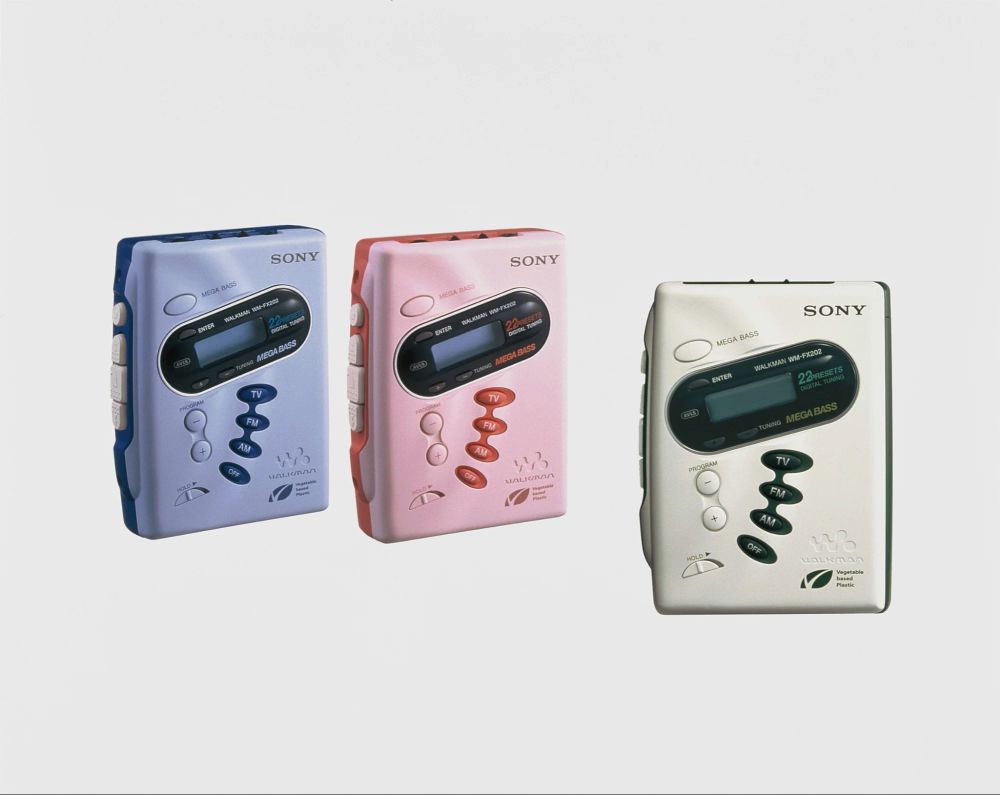
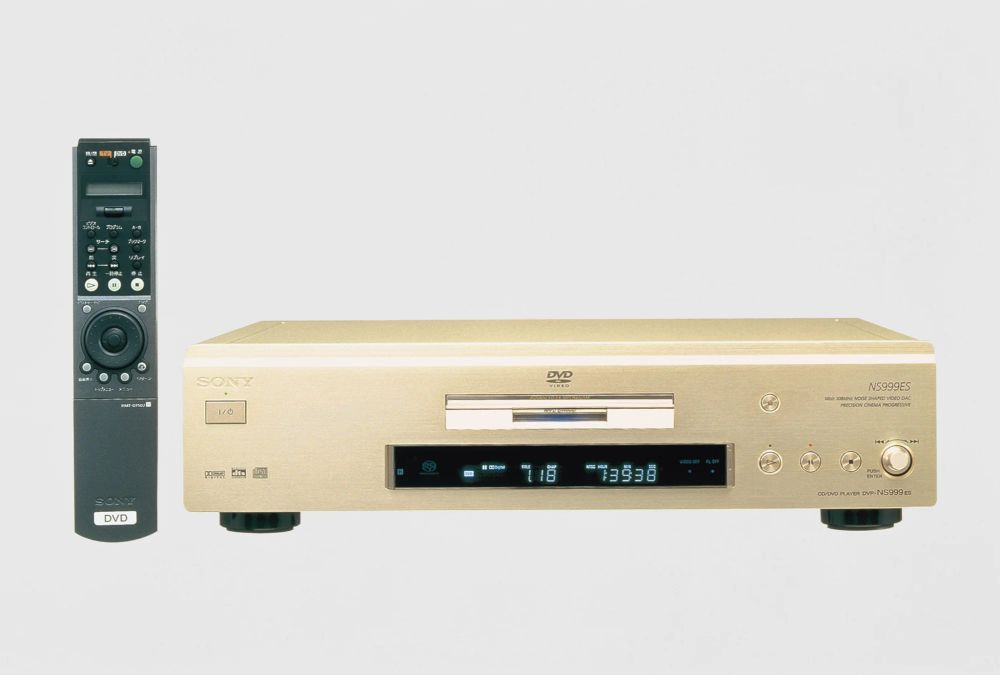
小林:最初に植物原料プラスチックが使われたのが2002年で、DVDプレーヤーやウォークマンが対象だったと聞いて驚きました。ウォークマンはソニーの看板商品だから、社内のハードルもさらに高かったんじゃないかなと。
藤平:それはもう…(笑) 。ウォークマンに使われたのは、トウモロコシから作られるポリ乳酸をベースとしたプラスチックです。上司と一緒に「やるからには胸を張って植物原料プラスチックと言えるものにしよう」と、植物比率51%以上であることにこだわりました。初めて任された開発だったので、製品化されたときは嬉しかったですね。
植物原料プラスチックのポリ乳酸は、石油由来とくらべて「熱や湿度に弱い」のが弱点。もともと備わっている生分解の性質をコントロールする必要がありました。使用中は、強度を維持する必要があったため、いくつもの改質検討を行いました。
小林:移動しながら使うウォークマンは、丈夫でないと困りますものね。
藤平:そうなんです。次に製品化されたDVDプレーヤーも、克服すべき課題がたくさんありました。内部部品は基本性能に加えて、燃えにくい性能を付与する必要があったため、環境負荷の少ない難燃剤の使いこなしなど、チャレンジングな開発に取り組ませていただいたと思っています。
協力しながら開発していくものづくりに魅せられ事業部へ。再生プラスチックで「映画館の音」を再現したい
藤平:ただ残念ながら、植物原料プラスチックは加工性にも課題があり、継続して使っていくことは難しかったんです。
でも私は、このときの経験が忘れられなくて。設計の方や、他の部署の皆さんと協力していくなかで、改めてものづくりの面白さを知り、もっと追求してみたくなったんですね。それで2013年に、オーディオ事業部の音響材料開発チームに異動しました。最初に取り組んだ製品もウォークマンでしたし、オーディオの部署とは縁を感じました。
小林:研究所から事業部に移るとなると、カルチャーもかなり違うでしょうし、色々と大変そうですね。
藤平:開発のスピードや、スケジュールのタイトさには驚きました。研究所では一つのテーマに長期的に取り組むことが許されるけれど、事業部ではある程度の期間で成果を出さなければいけない。製品が生み出される過程で、コストダウンの努力がいかに重要なのかも痛感しました。事業部では日々いろいろなことが起こるので、皆さん問題解決のプロというか、いつもポジティブに難題に立ち向かっていく姿勢が刺激的です。
小林:オーディオの部署では、再生材の音の課題を解決して、ホームオーディオの製品に使えるように尽力されたと伺っています。
藤平:はい、今日は再生材の原料のサンプルを持ってきたので、ぜひ手に取ってみてください。
小林:わぁ、カラフル!キラキラしていてきれいですね。
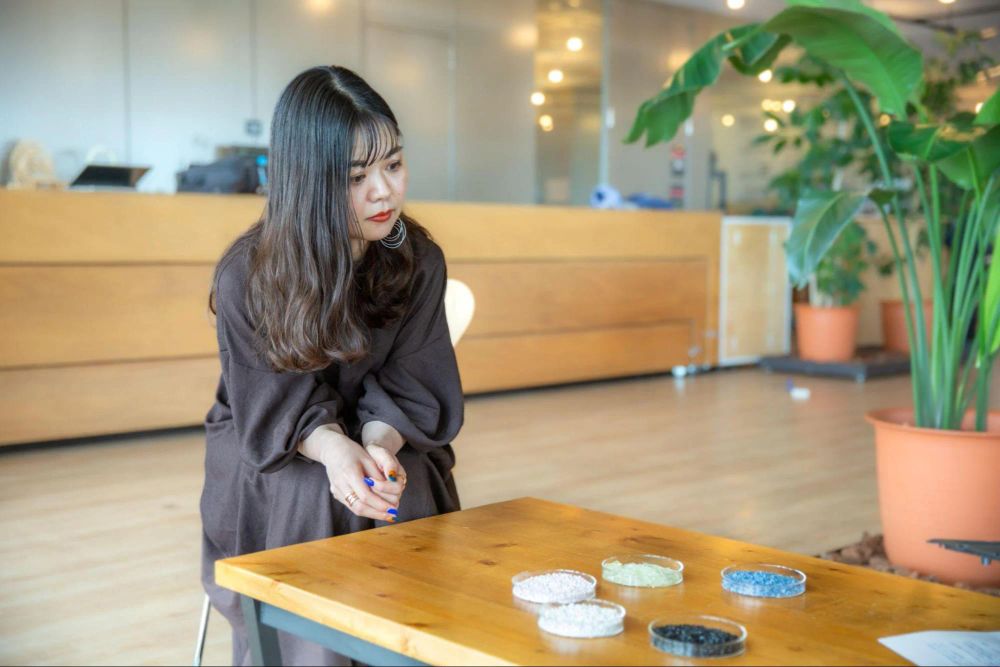
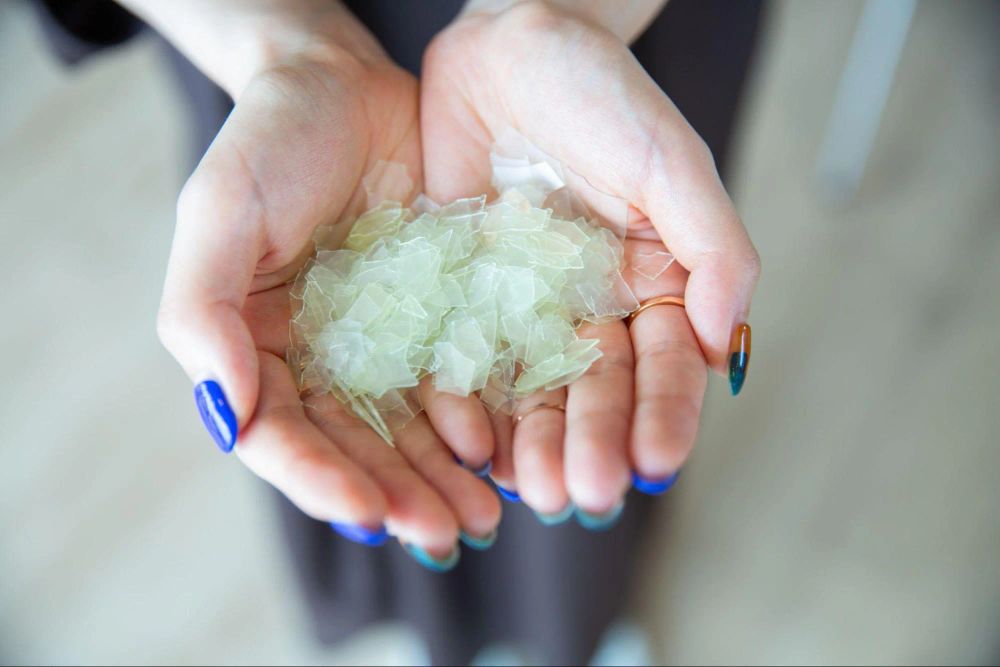
藤平:透明とブルーが再生原料です。透明の方は、元はディスクで、ブルーはウォーターサーバーの水ボトル。廃品回収されたものを洗浄し、ディスクは上に貼られた膜を全部はがして、原材料だけをフレーク状に加工しています。
ピンクと黒と白の粒は、この再生原料にバージン材や難燃材などを混ぜ合わせ、ペレット状にして、すぐに製品に使えるようにしたものです。
小林:オーディオ製品はカラーバリエーションが豊富だから、色々な色が必要なんですか?
藤平:再生原料は管理が難しくて、白色に着色すると異物により黒点が発生する可能性があるので、スタンダードは黒なんです。そこにあえて色をつけることにチャレンジした試作品もあります。
小林:すごい、未発売のサンプルなんですね。そちらの黒い板のようなものは…?
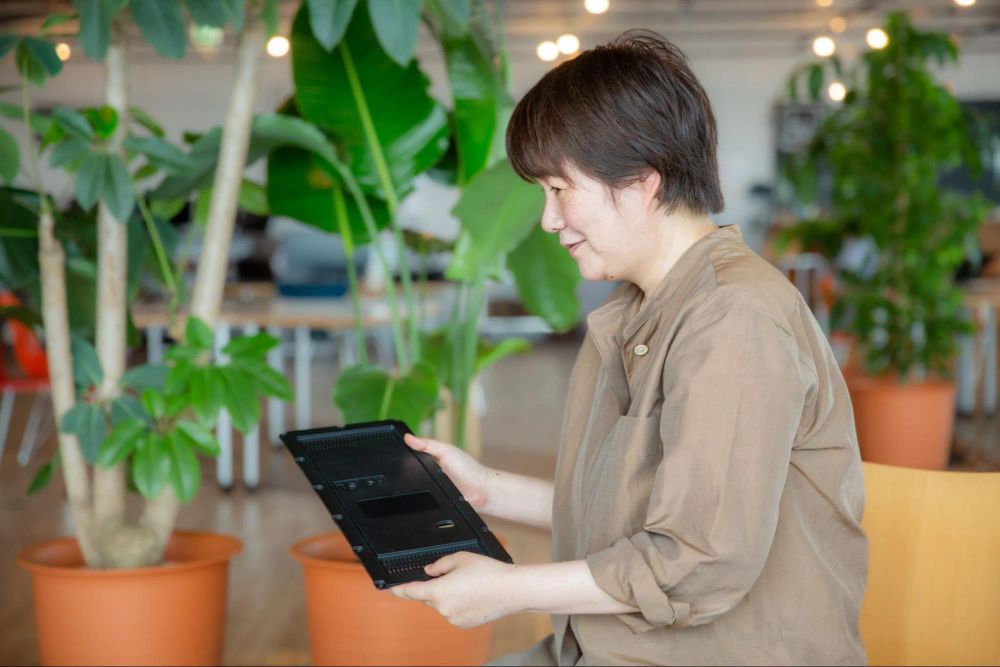
藤平:ソニーのサウンドバーという商品に付属する、サブウーファーのリアパネル(後ろのパネル)です。再生材で作られたもので、これは試作品ですが、実際に量産されて市場に出ています。
サウンドバーはオーディオの中でも、映画館の音を自宅で再現することにチャレンジしている商品です。再生材を導入するにあたり、今までサウンドバーに使用していた樹脂と同等以上の音質を維持する素材に仕上げるという、大きな挑戦がありました。
小林:最高の音質を提供するとなると、再生材に関わらず開発のハードルが高そうです。
藤平:そうですね、部品の素材を変えると音質も変わってしまいますから…。特に私が音響チームに来た当時は、再生材に対して音質に懸念があったような気がします。まずはそこを払拭するために、クリアな音、広がりがある音など、音響のエキスパートの方々の言葉を一つひとつ理解し、素材、配合に落とし込んで、実現していきました。
小林:私も学生のときは、無機材料を合成して評価する研究を小規模ながらやっていたので、プロジェクトの難しさが想像できます。新しい素材を開発して、コストも考えながら量産にもっていく、製品化するというのは、本当に大変なことですよね。
藤平:開発しても使ってくれる人がいないと、自己満足で終わってしまいますから。色々な部署のメンバーとコミュニケーションを取りながら、皆さんが何を望んでいるのかという情報を早く知ることと、正しく開発内容を伝える努力が必要だと感じましたね。
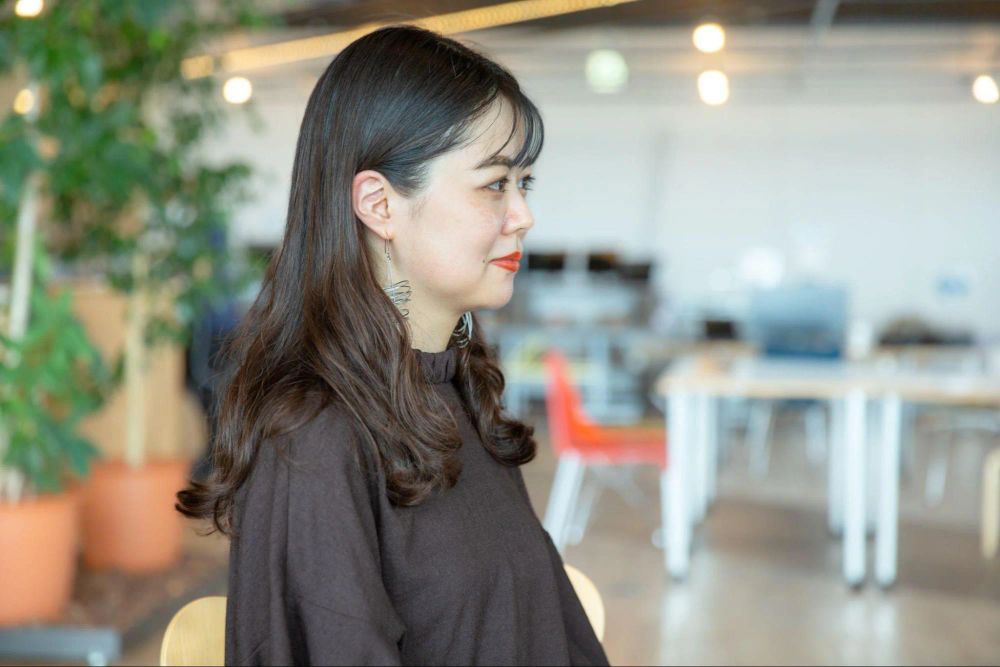
開発に20年。チャレンジできる場があることの大切さ
小林:今は企業のサプライチェーンに対する責任感や、サステナビリティをどう推進しているかが、お客様や外部の方から評価される大きなポイントになっていますよね。私が所属する調達部署も、パートナー企業を選定するときは、このような視点のあるなしも基準の一つとしてチェックしています。再生プラスチック素材が多くの製品に導入されていることは、ソニーの環境問題に対する姿勢の表明にもなっていると思うんです。
藤平:私たちはものづくりをしていく中で、地球の資源やエネルギーを使わせていただいている。そのことを忘れてはいけないという思いは、ソニーに深く根付いていますよね。
今ソニーの独自技術として注目されている再生プラスチックの SORPLAS™(ソープラス)や、籾殻由来の多孔質カーボン素材 Triporous™(トリポーラス)※ といった素材も、開発がスタートしたのは2000年代です。この二つは私の古巣である環境技術部で開発されていたものなので、 長い時間を経てようやく自社製品に採用されたり、 社外にも提供されたりするようになってきたことが本当に嬉しいです。 あきらめなかったかつての同僚たちもすごいと思うし、ソニーにはこのようにチャレンジができる場があると感じています。
プラスチック素材はネガティブに捉えられがちですが、素材としては安価ですし、加工性や利便性に優れています。やはり今後も私たちが生活していく上では、プラスチックと共存していく道があるのではないでしょうか。昨今は海洋プラスチックの問題が深刻化していますが、不用意に捨てられてしまうことを防ぐためにも、回収やリサイクルのシステムの構築に世界規模で取り組んでいかなければならないと思います。
私個人としては、サステナビリティへの取り組みを一過性のブームで終わらせないためにも、環境問題の解決に貢献できる技術をもっと開発したい。まだ誰も取り組んでいないような研究にも、どんどんチャレンジしていきたいと考えています。
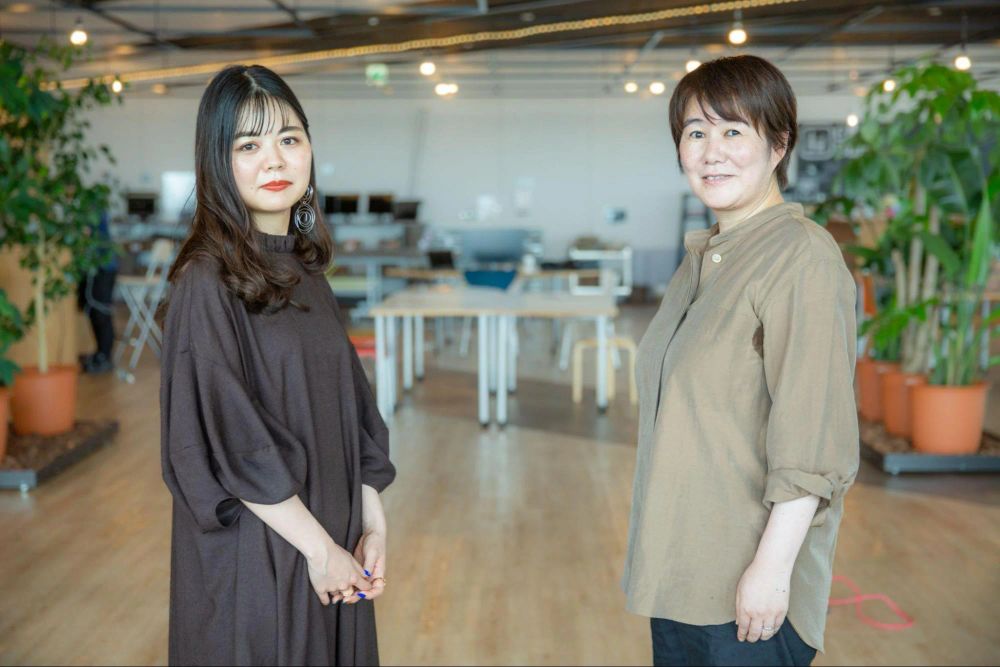
後輩記者のTakeaway
・より早く、正確なコミュニケーションが信頼関係をつくる
社外の方との折衝が多く、相手にご理解いただけるよういかに丁寧に会話するかが課題だった私。開発を自己満足で終わらせないために「早く、正しく」コミュニケーションを重ね、信頼関係を築いたという藤平さんのストーリーが刺さりました。
・素材開発に、失敗はつきもの
難問続出の素材開発。行き詰まったときは、どうやってモチベーションをキープするんですか?と尋ねたら、「日の目を見なかった研究の方が多いくらいだから、失敗してもへこみません。何かしらがんばってやっていればどうにかなる」と藤平さん。一歩ずつ積み重ねてきた20年が、再生プラスチックの利用拡大につながったのだと、はっとしました。
・テクノロジーを持つ企業には責任がある
今後、環境問題への姿勢は企業の価値をはかる物差しになると思います。人間は今まで、自分たちの生活のためにテクノロジーを進化させ、地球の自然に影響を与えてきました。でも今度は逆に、テクノロジーの力で環境負荷を削減できるかもしれない。ソニーのように技術力を持つ企業には、大きな責任があると感じました。